Kokerei

Beispiel für eine moderne Hüttenkokerei: Kokerei Schwelgern (Carbonaria) in Duisburg-Schwelgern

Kokerei Prosper in Bottrop: Von ArcelorMittal betriebene Bergwerkkokerei. Ansicht mit Löschturm und Niederdruckgasbehälter (Bauart Thyssen)

Blick in einen Kammerofen (1976, Wales)

Kammerofen: Detail (1942, USA)
In einer Kokerei wird aus Kohle mittels eines trockenen Destillationsverfahrens Koks und Rohgas erzeugt. Es werden die flüchtigen Bestandteile in der Kohle durch das Erhitzen auf eine Temperatur von 900 °C und 1400 °C pyrolysiert, freigesetzt und abgesaugt. Seit etwa 70 Jahren hat sich die Regenerativfeuerung, bei der die freigesetzten Bestandteile zur Befeuerung der Koksöfen benutzt werden, durchgesetzt. Auf dem fertigen Koks entsteht dabei eine Ascheschicht.[1] Durch das Entgasen der Kohle bildet sich ein poriger Koks, der fast ausschließlich Kohlenstoff enthält. Das Rohgas wird durch fraktionierte Kondensation in die Kohlenwertstoffe Teer, Schwefelsäure, Ammoniak, Naphthalin, Benzol und Kokereigas zerlegt, die in chemischen Werken weiter aufbereitet werden. In Deutschland sind derzeit (2017) noch fünf Kokereien in Betrieb.
Koks wird im Hochofen zur Erzeugung von Roheisen (Stahlgewinnung) benötigt. Das ist der heutige Hauptverwendungszweck. Der Schwefelanteil ist durch Vergasung erheblich reduziert, bei der Verbrennung des Kokses wird daher weniger Schwefel freigesetzt. Schwefel ist in der Anwendung im Hochofen unerwünscht, da er die Qualität der Eisenschmelze erheblich vermindert. Die mineralischen Aschebestandteile des Kokses bleiben gegenüber der Rohkohle unverändert.
Inhaltsverzeichnis
1 Geschichte und Grundlagen
2 Betriebsablauf
2.1 Benötigtes Personal/Arbeitsplätze
3 Die schwarze Seite
3.1 Koksofen
3.2 Ofendecke
3.3 Kohlenbunker
3.4 Maschinenseite
3.5 Koksseite
3.6 Kokslöschung
3.6.1 Koksnasskühlung
3.6.2 Kokstrockenkühlung
4 Die weiße Seite
4.1 Nebenprodukte
5 Kokerei aktuell (2005)
6 Industriepolitik
7 Verwandte Artikel
8 Literatur
9 Einzelnachweise
10 Weblinks
Geschichte und Grundlagen |
In den Anfängen der Eisenerzeugung wurde ausschließlich Holzkohle für die Verhüttung von Erzen eingesetzt.[2] Unbehandelte fossile Kohle (Braun- und Steinkohle) oder unverkohltes Holz sind dazu nicht geeignet, da die notwendigen hohen Temperaturen nicht erreicht werden und aufgrund der geringeren Reinheit der Brennstoffe keine ausreichende Roheisenqualität erreichbar ist. Durch den Bedarf an Holz, welches in einem ganz ähnlichen Verfahren wie bei der Kohleverkokung in Holzkohle umgewandelt wurde, veränderten durch die Abholzung riesiger Baumbestände ganze Landstriche ihr Aussehen. Erst im 18. Jahrhundert wurde die Kohleverkokung entwickelt, die fossile Kohle als Grundstoff einsetzt. Der neu entstandene Brennstoff löste die Holzkohle ab und ermöglichte erst die heutige Massenproduktion von Roheisen.
Durch die Erhitzung von Kohle unter Luftabschluss wird der Brennstoff Koks erzeugt, der spezifisch kohlenstoffreicher, reiner und von gleichmäßigerer Qualität ist als der Rohstoff Kohle.
Durch die kontrollierten Bedingungen im Kokereiprozess kann das Produkt Koks je nach Verwendungszweck an bestimmte Anforderungen angepasst werden wie
- Wassergehalt,
- Aschegehalt,
- Schwefelgehalt,
- Korngröße,
- Festigkeit,
- Abrieb.
Die häufigsten Endprodukte sind heutzutage Hochofen- und Gießereikoks.
Eine der wichtigen Eigenschaften des Hochofenkokses ist die Festigkeit auch bei hohen Temperaturen. Neben der Aufgabe, als Brennstoff zu dienen, stützt der Koks im Hochofen die gesamte Materialsäule aus Erz und Zuschlagstoffen. Kohle an seiner Stelle würde verbacken und die Durchlüftung des Gemisches erschweren.
Betriebsablauf |
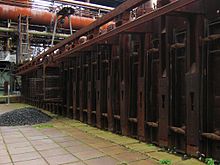
Koksofenbatterie der Hüttenkokerei der Völklinger Hütte

Füllwagen auf der Ofendecke
- Anlieferung/Mischen/Mahlen/Bunkern der Rohkohle
- Abholen einer Ofenbefüllung mit dem Füllwagen auf der Ofendecke
- Öffnen der Füllöffnungen auf der Ofendecke
- Schüttvorgang der Kohle in einen einzelnen Koksofen
- Je nach Ofenprinzip/Kohlequalität wird die Kohle gestopft
- Luftdichter Verschluss des Ofens
- Erhitzung
- Es folgen Ausgasung und das Erreichen der richtigen Porosität
- Öffnen der vorderen und hinteren Ofentür
- Ausdrücken
- Löschen und gleichzeitig Neubefüllung des Ofens
Nachdem ein Ofen befüllt ist, fährt der Füllwagen wieder zum Kohlenbunker und der Vorgang beginnt mit einem anderen Ofen von vorne. Die Betriebsabläufe sind so aufeinander abgestimmt, dass alle paar Minuten ein Ausdrückvorgang stattfinden kann. Die Ofenwände werden kontinuierlich mit dem beim Kokereiprozess entstehenden Gas beheizt. Je nach Zieleigenschaften des Koks und Ofengröße liegt die Backdauer zwischen 15 und über 30 Stunden.
Benötigtes Personal/Arbeitsplätze |
Für einen reibungslosen Betrieb der schwarzen Seite sind folgende Arbeitsplätze mindestens zu besetzen:
Füller – fährt den Füllwagen
Einfeger – schließt und vergießt die Fülldeckel, fegt die Decke sauber; mindestens ein, oft sogar zwei Mitarbeiter
Türensteller-Maschinenseite (MS) – bedient den „Türöffner“ an der Drückmaschine und reinigt den Meistergang
Drückmaschinist – fährt und bedient die Drückmaschine
Türensteller-Koksseite (KS) – fährt und bedient den KKF-Wagen; reinigt den Gang vor den Öfen
Löschwagenfahrer (bei Nasslöschung, heute seltener) – bedient den Löschwagen; reinigt den Löschturm, so weit ebenerdig möglich
Rampenzieher – bedient die Koksrampe, d. h. der Koks aus dem Löschwagen wird auf ein Transportband gesteuert, das zur Sieberei führt
Vorarbeiter – leitet und koordiniert die Betriebsabläufe der Batterie nach Anweisung des Koks- oder Gasmeisters
Koks-/Gasmeister – verantwortliche Aufsichtsperson für mindestens eine Koksofenbatterie
Die schwarze Seite |

Gasvorlage
Auf der sogenannten schwarzen Seite einer Kokerei findet die eigentliche Produktion des Kokses statt. Während der Arbeit in diesem Bereich entstehen Stäube und Abgase, die zur Namensgebung führten.
Koksofen |
Der Koksofen ist der zentrale Bestandteil einer Kokerei. Die zumeist verwendeten Horizontalöfen (Bewegungsrichtung beim Koksausdrücken) sind in der Regel mehrere Meter hoch und tief, aber nur ca. ½ m breit. Modernste Ofenkammern haben ein Volumen von bis zu 100 m³ (z. B. 0,5 × 6 × 32 m). In der Regel werden diese Kammern zu einer sogenannten Ofenbatterie zusammengefasst, wobei die Ofenkammern immer zwischen Heizzügen angeordnet werden, in denen bei 1200 bis 1400 °C Gase verbrannt werden und so die Ofenwände erhitzen. Das Heizgas entstammt der Gasreinigungsanlage, die zugleich die Nebengewinnungsanlage ist. Ist ein Hochofenbetrieb in der Nähe, dann wird das Gichtgas mit dem niedrigen Heizwert verwendet, wobei dann Koksgas mit hohem Heizwert beigemischt wird. Die Unterfeuerung wechselt etwa alle halbe Stunde zwischen Maschinenseite und Ausstoßseite hin und her, damit eine halbwegs gleichmäßige Erwärmung der Kammern erreicht wird.
Nach der ersten Anfeuerungsphase von ca. drei Monaten bei Inbetriebnahme einer Kokerei findet der Heizprozess kontinuierlich statt. Eine zu schnelle Beheizung oder sofortiges Abschalten der Befeuerung einer Batterie führt unweigerlich zu starken thermischen Spannungen, welche die Anlage irreparabel zerstören.
Die Koksöfen sind ähnlich wie ein Hochofen im Inneren mit hitzebeständigen Schamott oder Silikasteinen ausgemauert.
Jeder Ofen hat drei für den Betrieb wichtige Öffnungen, die vordere und hintere Tür an den Stirnseiten, die so breit wie die Kammern sind, sowie mindestens eine Füllöffnung auf der Ofendecke zur Beschickung des Ofens mit Kohle, meist aber vier bis fünf, um die Kohle möglichst gleichmäßig in den Ofen zu bringen und zu verteilen. Das Glattschieben der eingebrachten Kohle wird mit einer Planierstange durchgeführt. Diese Planierstange befindet sich an der Drückmaschine und wird von dieser in Gang gesetzt.
Ofendecke |

Ehemalige Maschinenseite der Kokerei des Essener Weltkulturerbes Zollverein
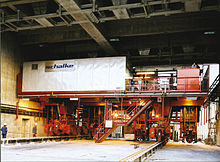
Füllwagen der Kokerei Schwelgern, Schalker Eisenhütte
Die Ofendecke ist nicht einfach nur das Dach einer Koksofenbatterie. Auf der Ofendecke fährt der Füllwagen zwischen den einzelnen Füllöffnungen der Koksöfen und einem oder mehreren Kohlebunkern hin und her.
Der Arbeitsplatz auf der Ofendecke ist nicht ungefährlich. Hitze, Staub, Gase und Flammen erschweren die Arbeit.
Kohlenbunker |
Je nach Anlagenbauart befinden sich auf der Ofendecke oder an einem der Enden einer Batterie eine oder mehrere Kohlenbunker. Ein Bunker enthält die Kohlevorräte, die von den Füllwagen in die Öfen verbracht werden. Die Bunkerkohle ist ein auf die Zieleigenschaften des Koks abgestimmtes Gemisch verschiedener Kohlesorten, die zuvor bereits durch Siebung oder Mahlung eine bestimmte Körnung erhalten hat.
Maschinenseite |
Unter Maschinenseite versteht man die Seite einer Koksofenbatterie, auf der die Drückmaschine (auch „Drücklok“ genannt) läuft (fährt). Die Drückmaschine hat die Aufgabe, den fertigen Kokskuchen (die unter Luftabschluss gegarte Kokskohle) zur Weiterverarbeitung auszudrücken. Hierzu wird eine Stange benutzt, welche sehr häufig zwei- bis dreigeteilt ist, um die gesamte Länge des Ofens befahren zu können. Am vorderen Ende dieser Stange befindet sich der Drückkopf. Der Gang vor den Öfen auf der Maschinenseite wird Meistergang genannt. Dieser Maschinenseiten-Gang ist so breit, dass hier nicht nur der „Türensteller“ seiner Arbeit nachgehen kann, sondern auch der „Koksmeister“ (auch „Gasmeister“ genannt).
Koksausdrückmaschine der Kokerei Schwelgern, Schalker Eisenhütte
fahrbare Bühne der Kokerei Prosper
Stempel zum Ausdrücken vor …
… und nach Einfahren in den Ofen
Koksseite |
Die Koksseite ist jene Seite einer Koksofenbatterie, an der der gare Koks aus dem Ofen fällt und mit Hilfe einer Überleitmaschine in den Löschwagen gelangt. Damit dies problemlos geschehen kann, fährt hier der „Koks-Kuchen-Führungswagen“, auch KKF genannt. Ein Maschinist (Türensteller) bedient die Maschine und fährt zu dem entsprechenden Ofen. Wenn alle Sicherheitssignale auf grün sind, wird mit dem KKF die Tür geöffnet. Der KKF fährt dann die „Wanne“ in Position. In modernen Kokereianlagen wird dieser Vorgang vollautomatisch gesteuert. Diese Wanne ist lediglich die Führung für den Kokskuchen, vom Ofen über den Gang zum Löschwagen.
Überleitmaschine der Kokerei Schwelgern, Schalker Eisenhütte
Löschfahrzeug der Kokerei Schwelgern
Löschbühne der Kokerei Prosper
Befüllung des Waggons
Fahrt zum Löschturm
Kokslöschung |
Ein Unterscheidungsmerkmal der Prozessführung ist die Art des Kokslöschens.
Sobald durch das Öffnen der Kontakt zum Luftsauerstoff hergestellt ist, beginnt der Koks bei den noch herrschenden Temperaturen zu verbrennen. Um das zu verhindern, muss er schnell gelöscht und abgekühlt werden.
glühender Koks auf dem Weg zum Löschen
im Nassverfahren gelöschter Koks
zur Kontrolle verbleibt der gelöschte Koks eine Zeit lang im Bunker
Diese Abkühlung kann auf folgende Arten geschehen:
Koksnasskühlung |
- Pro Tonne Koks sind ca. 2 m³ Wasser zur Löschung notwendig.
- Wärmeenergie geht verloren.
- ca. ein Drittel des Löschwassers verdampft.
- Problematische Reinigung des vor allem mit Staub, Wassergas und Schwefelwasserstoff verunreinigten Wasserdampfes
Noch 1986 lagen die Messwerte für einen Koksnasskühlvorgang bei 200 bis 2000 g Staub pro Tonne Koks. Im modernen CSQ-Verfahren (Coke Stabilizing Quenching) rechnet man nur noch mit einer Belastung von 10 bis 15 g/t.
Kokstrockenkühlung |
(meist mit Stickstoff als Inertgas)
- ermöglicht Energierückgewinnung (Wärme, Stromerzeugung)
- kein Wasserverbrauch
- geringere Staubentstehung
- höhere Koksqualität durch niedrigeren Wasseranteil
- teuer im Bau und Unterhalt
Die Trockenkühlung amortisiert sich nach [3] 3 bis 5 Jahren.
Die weiße Seite |
Hauptartikel: Kohlenwertstoffanlage
Mitte des 19. Jahrhunderts begann man aus den Kokereigasen wertvolle Rohmaterialien für die Chemie-Industrie zu gewinnen. Die Anlagenteile, die die Aufgabe der Gaswäsche und Abscheidung verschiedener Stoffe übernehmen, werden meist auf der Maschinenseite gebaut und durch dicke Rohrleitungen der Gasvorlage mit dem Kokereigas versorgt. Hier fallen normalerweise keine Stäube oder andere sichtbare Verschmutzungen an, daher der Name „weiße“ Seite oder Kohlenwertstoffanlage. Um das Rohgas von der Gasvorlage abzusaugen und dann durch die Nebengewinnungsanlagen zu fördern, wird ein als Gassauger bezeichnetes Gebläse eingesetzt. Hierbei ist es entscheidend, die Gasvorlage unter leichtem Überdruck (rund 2 mbar bis 5 mbar) zu halten. Ein Unterdruck würde das Eindringen von Luftsauerstoff begünstigen und somit ein Explosionsrisiko bewirken. Ist der Gassauger gestört, wird abgefackelt.
Zuerst wird das Kokereirohgas heruntergekühlt und anschließend in sogenannten Gaswäschern gewaschen. Darauf folgend werden die einzelnen herausgewaschenen Bestandteile der Weiterverarbeitung zur Herstellung folgender Nebenprodukte den jeweiligen Produktionsprozessen zugeführt:[4]
Nebenprodukte |
- Teer
- Benzol
- Schwefel
- Ammoniak
Ammoniumsulfat (Düngemittel), seltener Ammoniumnitrat (auch als Düngemittel)- Schwefelsäure
- Phenolatlauge
Kokerei aktuell (2005) |

Kokerei Prosper mit aktivem Löschturm
Kokerei Schwelgern GmbH
Der Weltmarktpreis für Koks schwankt stark. Von 2002 bis 2004 stieg der Weltmarktpreis für chinesischen Koks im Zuge der weltweiten Stahl-Hausse von etwa 80 US-Dollar auf etwa 350 US-Dollar, mehr als eine Vervierfachung des Preises, dreimal so viel wie die Steigerung des Stahlpreises im gleichen Zeitraum.
Parallel bauten Chinesen im Ruhrgebiet die moderne Kokerei Kaiserstuhl in Dortmund ab.[5] Dem letzten Werk in Deutschland mit Kokstrockenkühlung hatte der gesicherte Absatz gefehlt, nachdem der Thyssenkrupp-Konzern seine Roheisen- und Stahlerzeugung in Dortmund eingestellt und in Duisburg konzentriert hatte.
Die drei im Raum Ruhrgebiet verbliebenen Kokereien, das Bottroper Werk Kokerei Prosper, die Kokerei Schwelgern und die Kokerei der Hüttenwerke Krupp Mannesmann, arbeiten seit drei Jahren an der Kapazitätsgrenze. Für die Kokerei der Hüttenwerke Krupp Mannesmann im Duisburger Süden (Huckingen) wurde am 3. Juni 2005 ein Genehmigungsantrag für die Erweiterung um eine weitere Batterie bei der Bezirksregierung Düsseldorf gestellt. Die Genehmigung wurde am 13. Januar 2006 erteilt. Am 29. März 2014 wurde der erste Koks gedrückt und die Erweiterung der Kokerei damit in Betrieb genommen.
Im Dezember 2005 wurde die Sanierung der Zentralkokerei Saar GmbH, Dillingen beschlossen. Das Konzept sieht den Bau einer neuen dritten Batterie vor. Nach deren Inbetriebnahme wird die alte Batterie Nr. 1 abgeheizt und neu aufgebaut. Danach geht die zweite alte Batterie
außer Betrieb.
Industriepolitik |
Infolge des starken Anstiegs der Kokspreise meinen einige Kohlebefürworter, es sei nun wieder wirtschaftlich, in Deutschland Kohle zu fördern und neue Schächte abzuteufen. So existieren Pläne für ein neues, angeblich subventionsfrei zu erstellendes Bergwerk nördlich Hamm, deren Verwirklichung jedoch auf Grund der hohen Investitionskosten als unwahrscheinlich gilt.[6] Skeptiker sehen bei einer Investition im derzeitigen Wirtschaftszyklus schon jetzt wieder volkswirtschaftliche Folgekosten durch die nächste Absatzkrise. Außerdem ist derzeit noch offen, ob die Förderung ohne Subventionen möglich sein wird.
Verwandte Artikel |
- Liste von Kokereien in Deutschland
Literatur |
Handbuch der Gasindustrie, insbesondere Band 1 „Gaserzeugungsöfen“, Dr.-Ing. Horst Brückner u. a., Verlag R.Oldenbourg München/Berlin 1938- Walter Buschman: Zechen und Kokereien im rheinischen Steinkohlenbergbau. Aachener Revier und westliches Ruhrgebiet. Mann, Berlin 1998, ISBN 3-7861-1963-5
- Dietmar Osses: Kohle, Koks, Kultur. Die Kokereien der Zeche Zollverein. Stiftung Industriedenkmalpflege und Geschichtskultur, Dortmund ca. 2002, ISBN 3-935783-09-4
- Franz Michael Ress: Geschichte der Kokereitechnik. Glückauf, Essen 1957
- Fritz Schreiber: Entwicklung und gegenwärtiger Stand der Kokereiindustrie Niederschlesiens. Springer, Berlin 1911 (Digitalisat)
- Michael Farrenkopf (Hrsg.): Koks. Die Geschichte eines Wertstoffes, 2 Bde. Deutsches Bergbau-Museum, Bochum 2003.
Einzelnachweise |
↑ Uhde: Competence and know-how by tradition - A new dimension in cokemaking technology (PDF; 3,9 MB)
↑ Rolf Peter Sieferle: Der unterirdische Wald. Energiekrise und industrielle Revolution. München 1982
↑ Case Study of Technology Transfer between Japan and China in iron/steel industry (Memento vom 12. Mai 2006 im Internet Archive)(in Englisch; PDF; 3,3 MB)
↑ Theo Payer, Wilhelm Baum: Gasreinigung und Nebenproduktgewinnung (PDF; 5,0 MB)
↑ Stefan Willeke: „Herr Mo holt die Fabrik – Die modernste Kokerei der Welt zieht von Dortmund nach China“ In: DIE ZEIT Nr. 40 vom 23. September 2004
↑ wa.de: Pläne für einen Förderstandort Donar gehören endgültig der Geschichte an, 7. Februar 2013.
Weblinks |


- Bilder von Kokereien in Europa und Nordamerika
Kokerei Schwelgern – Interaktives Panorama – auch in großen Bildformaten- Fotografien von Kokereien
Kokerei August Thyssen – Ausführliche Beschreibung, zahlreiche Fotos und Abbildungen- Video eines Drückvorgangs